A certain electrical appliance manufacturing company (hereinafter referred to as A company) specializes in the production and sales of audio-visual electronic products such as video recorders, VCD players and DVDs; it is also one of the largest production bases for PCB boards in China. After obtaining the ISO9002 international and domestic double-qualified quality assurance system certification, in order to further win by quality in the fierce market competition, barcodes are applied to the production quality management tracking system.
First, the main goal of the system
Four main goals to be achieved by the system:
- Quality tracking: It can track the model (mainboard, power supply and CDROM board) of the whole machine and the main substrate (PCB board), production site, production date, team production line, PCB board version number, engineering change (ECO), batch And serial number and other information.
- Real-time dynamic tracking of production: The actual production situation can be known from the computer at any time.
- Customer tracking: The customer’s name, address and shipment quantity can be obtained from the computer at any time.
- Report function: Provide various management reports for management review.
Two, development process
The entire development process can be divided into five stages, each stage has a detailed work plan.
Phase 1: Develop a specific plan
Barcode automatic recognition technology has the characteristics of fast input speed, high accuracy, low cost and easy operation. Company A uses barcodes to label the main components in the automated assembly production line and various processing processes. After being collected and decoded by the barcode reader, the barcode information is input into the database of the computer server. Each machine and main component will have a unique barcode. No matter where the machine is sent, there will be a record. If there is a problem, you only need to read the barcode on the warranty card, and you can call up all the relevant data of the product in the database, which greatly facilitates the quality tracking and after-sales service of the product.
A company’s barcode tracking system process
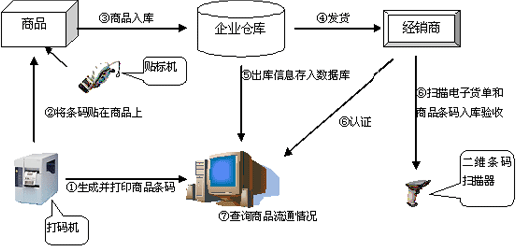
Phase 2: Finding a partner
Based on the establishment of detailed research and analysis, analyze the barcode system solutions and quotations of each barcode supplier. The provision of barcode software and hardware, after-sales service and consumables is as local as possible to reduce the investment in the barcode tracking system. Through comprehensive consideration of various factors, we will find a more suitable partner and sign a barcode implementation contract.
The third stage: database structure design, barcode design and programming
This system can contain four main databases: system design library, user library, PCB library and complete machine library. Barcode label paper must contain information: model/logo, production site, production date, production Team/production line. Batch number and serial number, and barcode tracking system software can accept different barcode format and size requirements. Barcode labels are used on PCB boards, complete machines, packaging boxes and warranty cards.
For example: when designing the barcode format for PCB boards, consider the model, production site, production date, production team, production line, batch number, and serial number.
Attachment: The physical label of the PCB board is as follows:
The barcode type uses the 39 code with verification, which is the most used in industrial production.
In addition, it is also necessary to consider 5,000 complete machines as a unit. When the serial number has accumulated to 5,000 units, the batch number is automatically incremented by one, and the serial number starts counting from one at the same time.
In this system, when unreasonable data is input by the scanner or keyboard, it is invalid operation. Try to eliminate human error and improve the reliability of the system.
The fourth stage: network cabling system and network system design
Computer and network systems are the material basis of the barcode tracking system. The network structure of the barcode tracking system implemented by Company A is shown in the attached picture. The computer network structure adopts ETHERNET network and star topology structure. Connect a barcode tracking server and 9 barcode printing or scanning workstations for production lines and warehouses with a twisted pair cable through a hub. In addition to the above-mentioned workstations, we also installed workstations for the general manager’s office, quality department, production department and material department. This ensures that decision makers can effectively grasp first-hand information and issue instructions, and staff can also inquire or process company production, inventory and quality information at any time.
The fifth stage: training and trial operation of the barcode tracking system
After more than half a year of operation of the barcode tracking system, it shows that the actual operation effect is good. The barcode tracking system software can be suitable for the system environment, and can currently meet the requirements of the system’s response speed: at the same time, it can complete the relevant work of the relevant departments of the enterprise on the barcode tracking system.
Three, system function design
The system is a modular structure, and you can choose to go deeper through the pop-up drop-down menu. The system consists of five main functional modules: system management, PCB board production management, assembly production management, warehouse management and other functions. Each main function module has its own sub-function module to perfect its function.
System Management
System parameter design, system database modification, operator management and password management.
PCB board production management
Print barcode: According to requirements, in addition to printing the barcode of the power supply and the CDROM board, two copies of the motherboard barcode will be automatically printed, one copy is pasted on the PCB board; the other copy is randomly used for the final assembly record, so that the barcode of the whole machine and its use The barcodes of the main PCB boards (main board, power supply and CDROM board) establish a one-to-one correspondence.
Barcode Scanning: Scan the barcode of PCB board to form PCB board library.
Statistical analysis: query and make statistics and form reports as required.
General assembly production management
Print barcode: Print the barcode on the whole machine, packing box and warranty card.
Barcode scanning: Scan the barcode of the whole machine and PCB board to form a finished product library.
Statistical analysis: query and make statistics and form reports as required.
Warehouse management
Warehousing registration: In the General Assembly Department, manually input the relevant data of the finished product warehousing.
Pre-scanning: receiving data, loading racks, not out of storage and clearing racks are equal to functional modules.
Outbound management: Generate outbound orders, and form outbound reports by scanning outbound products.
Statistical analysis: query and make statistics and form reports as required.
Other functions
Quality tracking: According to the barcode of the whole machine, query the main PCB board model (main board, power supply and CDROM board), version number, ECO and other data.
Query system: query various production conditions and quality information of the system, including daily output, weekly output, monthly output, stage output and inventory, PCB board version number and ECO data.
Report printing: Print various reports.
Other formats: The management software can accept different formats, that is, the way of bar code composition can be set by the user.
In addition to the above-mentioned main function modules, we will also add main function modules for the warehouse center and after-sales service.
- Warehouse center: warehouse management inside the factory and remote management outside the factory.
- After-sales service: Warranty card and maintenance record management.
Four. Experience
With the development of science and technology, the previous manual operation has become less and less suitable for the requirements of modern management under the new situation. The introduction of computer technology and barcode technology into the field of production quality management has become an inevitable trend, such as the original production schedule Tables and reports such as daily, weekly and monthly output are all made by manual statistics by multiple people. The labor intensity is high and the work is repetitive and cumbersome. After adopting the barcode tracking system, all the above-mentioned reports are automatically completed by the computer, which is simple, convenient, accurate and fast. Through data collection, management, retrieval, archiving, and real-time statistics, quality information and dynamic reflection of the production status enable production managers to understand the production situation in a timely, accurate and comprehensive manner, so as to take necessary and effective measures to ensure that the production can be The scheduled plan is proceeding normally. After the production line adopts the bar code management system, the quality and management level can be greatly improved, and it will bring significant effects to the decision-making and management of the enterprise.
The product, through the introduction and summary of the barcode tracking system of Company A, hopes to provide reference and help for the application of barcode technology in automatic production lines in the future.