In the 21st century of economic globalization, information globalization and capital globalization, logistics has become the focus of attention and is known as the “third source of profit” for enterprises. The warehousing industry is not only the main body of the traditional logistics industry, but also a very important part of the modern logistics industry. In the entire material flow process, storage costs account for a large proportion of the entire product circulation cost. The ultimate goal of improving the level of logistics management is to save product circulation costs. Therefore, it is necessary to improve the management level of the warehousing industry and regulate the warehousing industry market. The barcode technology is the key to warehouse management. This article introduces the high work intensity, slow speed, low efficiency and other issues of general warehouse management mode, introduces the important roles of barcodes in warehouse management, and focuses on how to use barcode technology to improve circulation speed in a modern warehouse environment. And work efficiency. Compared with traditional warehouse management methods, modern warehouse management under bar codes has incomparable advantages.
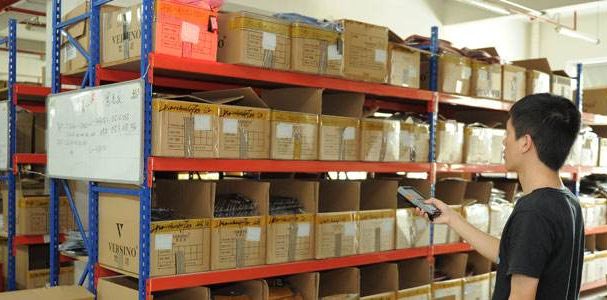
First, the development background of modern warehousing
With the rapid development of the modern economy and the increasingly strong individual and diversified needs of consumers, the life cycle of modern enterprise products has shortened and the speed of new products being put on the market has accelerated. Enterprises will inevitably transform from a small-variety, high-volume production method to a multi-variety, small-batch production method. This change requires the transformation of logistics activities from a small variety, large-volume logistics method to a multi-variety, small-batch, multi-batch and small-quantity mode. Therefore, the traditional storage warehousing method based on the concept of passive “storage” centered on improving storage efficiency is transformed to the modern circulation warehousing centered on improving the level of customer logistics services based on the concept of active “circulation”. Way changes. Under this trend, modern logistics treats the circulation of goods from the supplier to the end customer as a whole, which places high demands on the warehouse management activities themselves. Specifically, with the movement of commodity entities, two physical phenomena, “place transfer” and “time passage” will inevitably appear. Among them, “time passage” is in the process of close connection between production and sales, integration of circulation, and networking. Has become an important operating resource. Warehousing plays an indispensable role in the process of “time passing”, and modern warehousing management activities determine the level of logistics time efficiency. This warehousing method not only requires improved storage efficiency, but also requires timely, accurate, and rapid satisfaction of customer logistics service needs.
The transformation from traditional warehousing to modern warehousing puts forward higher requirements on warehousing management and also brings new challenges to warehousing operations. This challenge is manifested in the following three aspects.
- Increased the difficulty and refinement of warehousing operations
- Higher requirements are put forward for the efficiency and speed of operations
- Meet customer logistics services at a deeper level
Limitations of the traditional warehouse management model:
However, many enterprise warehouse management still remain on the basis of manual operation. All data entering and exiting the warehouse is entered, verified and determined one by one by the warehouse administrator. Under such conditions, the warehouse keeper’s operation errors will cause a series of problems. Moreover, this kind of warehouse management operation method seriously affects work efficiency. Many inbound and outbound data cannot be updated in the system in time, and effective location management is not implemented in system management. The system cannot always understand the material in the warehouse. Disadvantages such as the distribution status and the storage capacity of the warehouse. The summary is as follows:
1.1 Traditional warehouse management has high intensity, slow circulation, and low efficiency
First of all, traditional warehouse management implements a manual management model, which generally relies on a non-automated, paper-based system to record and track incoming and outgoing goods, and implement the internal management of the warehouse with human memory. This makes the administrator’s work intensity very high and prone to errors.
Secondly, traditional warehousing management adopts manual accounting method, using the ledger to understand the goods in and out of goods and inventory. For the entire storage area, human factors are uncertain, leading to low labor efficiency and serious waste of human resources. It is also impossible to know whether the account is consistent with the physical object in time and accurately. With the increase in the variety and quantity of inventory and the sharp increase in the frequency of in and out of the warehouse, it may create some items that cannot be supplied in time or are backlogged. The traditional warehouse operation mode seriously affects normal operation. efficient. It is also difficult to meet the requirements of fast, accurate and real-time warehouse management.
1.2 The planning of the warehouse and the placement of goods are unreasonable
Manually managed warehouses generally use disorderly placement of goods, resulting in chaotic delivery operations and high error rates, which is not conducive to product quality control and restricts the improvement of product quality; and the materials are not considered The problem of the transportation route is that there are important complex settings of equipment and personnel, so that resources cannot be effectively allocated. In addition, the “lifetime system” of material storage tools, materials of different specifications are placed on the same specifications of the shelf, lack of flexibility, Caused a great waste of space.
1.3 Management pressure and risks are high, and management costs remain high
Traditional warehouse management has directly led to the increase in the possibility of human error due to the large-scale adoption of manual operations, the high management pressure and management risk, and the high management cost. In the era of increasing modern logistics requirements, traditional management methods can no longer meet this requirement.
The above-mentioned drawbacks have seriously affected the efficiency of warehouse management and reduced the storage capacity of the enterprise’s warehouse, but it has increased the cost and manpower of warehouse management and restricted the development of the enterprise. In this trend, in order to further improve the efficiency of warehouse management and reduce the risks and costs of warehouse management, the use of information systems and barcode technology in warehouse management has unparalleled advantages.
The superiority of modern warehouse management under bar code
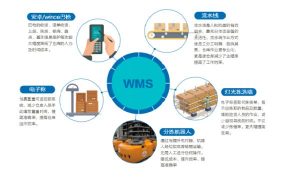
Modern Warehouse Management (WMS) is a warehouse management system controlled by a computer. Location inventory, inventory management, order processing, sorting and distribution control. Modern warehousing management focuses on the optimization and effective management of warehousing execution, and at the same time extends to transportation and distribution plans, and information interaction with upstream and downstream suppliers and customers, so as to effectively improve the execution of warehousing enterprises, distribution centers and warehouses of production enterprises. Efficiency and productivity, reduce costs, and improve the satisfaction of corporate customers, thereby enhancing the core competitiveness of the company. Generally, it has the following functional modules: management of individual order processing and inventory control, basic information management, cargo flow management, information reporting, receipt management, picking management, inventory management, warehouse transfer management, printing management and back-end service system.
Modern warehouse management system can also realize the consolidation and order distribution of different orders of the same customer through the back-end service program, and unify operations such as putting on shelves, picking, replenishment, inventory, and moving warehouses based on PTL, RF, and carton label methods. Dispatch and issue instructions, and receive feedback data from PTL, RF and terminal PC in real time. The entire software business is consistent with all aspects of enterprise warehouse logistics management, realizing real-time and effective control of inventory management.
The system completely integrates barcode technology into cargo management. After the barcode is introduced into the barcode warehouse management system, the steps of manually writing bills and sending to the computer room for input are removed, and the problem of outdated and lagging warehouse information is solved. No matter where the items go, they can be tracked automatically. The combination of bar code technology and information technology helps companies use warehouse space in a reasonable and effective manner. The bar code warehouse management system provides customers with the best service in a fast, accurate, and low-cost manner. The warehouse management information system software is powerful. With a high degree of completeness of functions, the system has fully considered various warehousing operation procedures, has been strictly defined, and is closely integrated with actual business. The summary is as follows:
- Strong reliability, flexible operation, convenient and easy-to-use: The system embodies humanization in the interface and function organization, and is convenient to operate, and greatly improves work efficiency through quick operation. Among them, the reading accuracy of barcodes far exceeds that of manual records. On average, an error occurs every 15,000 characters. The error rate of keyboard input data is 1%, and the error rate of using optical character recognition technology is 1%. The error rate of barcode technology is less than one part per million. The bar code reading speed is very fast. Compared with the keyboard input, the bar code input speed is 5 times that of the keyboard input, and it can realize “instant data input”.
- Management risks are reduced and management costs are low: Compared with traditional warehouse management, modern warehouse management uses an efficient system to process operations, and management risks are significantly reduced. In addition, the requirements for warehouse management personnel are reduced, which greatly reduces management costs. Barcode technology also only requires a small sticker and a relatively simple optical scanner, and the cost is quite low.
- The whole process of tracking the goods entering, leaving, and inventory, improving inventory accuracy. Real-time monitoring of inventory dynamics can effectively control abnormal inventory conditions, provide a scientific basis for management decisions, improve customer service response capabilities, and improve customer satisfaction. Barcode symbols can be manually entered by keyboard, and can also be combined with related equipment to form an identification system to achieve automatic identification, and can also be linked with other control equipment to achieve automatic management of the entire system. Moreover, the writing of bar codes is very simple, and the production only requires printing, which is called “printable computer language”.
- Good scalability: Adopt international standard data expression technology, object-oriented design method, and realize componentization so that the system has good scalability. The standardization of the warehousing process provides a unified operating platform for the collaboration between employees and departments.
Two, the specific application of barcode in modern warehouse management
(1) Goods warehousing
Before the goods are put into storage, the following preparations should be made:
First, scientifically code the warehouse locations and identify them with bar code symbols to realize warehouse location management. Scientifically encode the warehouse locations, use barcode symbols to identify them, and collect the incoming substances when entering the warehouse. At the same time, import the management system. Warehouse location management is conducive to quickly locating the location of inventory in warehouses or multi-variety warehouses, is conducive to achieving first-in first-out management goals and improving the efficiency of warehouse operations, thereby reducing warehouse management costs.
Second, scientifically code the goods, and print the barcode labels of the inventory according to different management objectives (for example, whether to track a single product or to achieve shelf life/batch management). On the basis of scientific coding, the barcode label of the goods is printed out before storage and pasted on the packaging of the goods to facilitate automatic data collection in the future.
Finally, when the designated goods are delivered to the warehouse, the warehouse management personnel will accept the goods according to the order, and use the handheld terminal barcode data collector to quickly and accurately complete the receipt data collection. When receiving the goods, the operator uses the handheld terminal to scan or enter the barcode of the goods and the actual quantity received according to the content of the receipt. The data is saved to the warehouse management system, and the warehouse personnel or management personnel can query the relevant receipt data. Data upload and synchronization Upload the collected data to the material management system, and automatically update the data in the system. At the same time, the updated data in the system can be downloaded to the handheld terminal for inquiries and calls on site. Specific steps:
- When the materials are in the warehouse, scan the barcodes of different goods and enter the corresponding contents of the barcodes into the system. In this way, by querying the barcode, you will see the storage time, unit price, storage location, supplier and other related information of the material. In the flow links such as the requisition of materials, as long as the barcode is scanned and the required quantity is written, other information will be automatically loaded. If the goods in the original package do not have a bar code, prepare the internal bar code and label the internal bar code on the corresponding product package without the original bar code after the goods arrive.
- After the goods are in the warehouse, arrange them in the corresponding location according to their classification and attributes, use the handheld terminal to scan the barcode of the product to be placed, and then scan the location barcode on the shelf (or directly enter the location number), and then enter Relevant information, such as: document number, package number, actual weight, etc. Make the goods of different barcodes correspond to the location of the warehouse, and improve the efficiency of inventory and picking.
- After all the goods are placed, connect the handheld terminal to the computer system, and transmit the goods’ arrival and inventory location data to the computer. Complete the final operation. The advantages of using barcode technology for warehousing:-Paperless receiving operation;-Check the difference between the manifest and the received goods to ensure the correctness of the received goods and data-Convenient to save the corresponding data and upload it back to the PC for update And query-quick operation, improve work efficiency
(2) Goods out of warehouse
The warehouse staff picks the goods at the designated place according to the requirements of the document, and sends the goods to the public delivery area, and uses the data collection terminal to scan the goods position and the barcode of the goods, and enter the actual quantity of goods shipped , (If the sent goods do not match the number of the outbound order, the terminal will automatically display and alarm to avoid wrong operations)
Warehouse personnel or management personnel can query relevant shipping data; specific steps;
- The warehouse management staff generates a delivery list according to the bill of lading, and prints the delivery list;
- The warehouse management personnel download the outbound order data to the handheld scanning terminal;
- When shipping, the shipper first scans the outbound order number and its order to be shipped;
- After ordering the goods correctly, load the goods away and complete the delivery;
- Through the handheld terminal verification, the delivery operation of the code complement can be carried out in time;
- Check the difference between the manifest and the shipped goods to ensure that the received goods and data are correct;
- Taking inventory-warehouse personnel or management personnel can query related shipping data on a regular or irregular basis.
- For material delivery, add a delivery list on the handheld terminal, and then scan the material barcode to handle the delivery of the material.
- Substance consumption workshops and teams use handheld terminals to consume substances to be used.
- When the material moving warehouse keeper moves the equipment to the storage location, first scan the material barcode with the mobile handheld terminal, and scan the original cargo location barcode of the substance and the current cargo location barcode at the same time, and the cargo location information of the substance is Recorded in the system.
(3) Inventory of goods
Inventory-is to check the goods in the warehouse regularly or irregularly, compare the difference between the actual inventory and the data list, and improve the accuracy of the inventory data. Its purpose is to:
- Determine the existing stock. Inventory can determine the actual inventory quantity of existing inventory goods, and make the inventory book quantity consistent with the actual inventory quantity through profit and loss adjustment. Due to many records, mistakes, and omissions, the inventory data records are not true. In addition, due to product damage, loss, inspection and delivery, the inventory is incorrect; sometimes the inventory method is improper, resulting in incorrect inventory, double inventory, and missing inventory. For this reason, it is necessary to check the inventory regularly, find out the problems and find out the reasons, and make adjustments in time.
- Confirm the profit and loss of corporate assets. The total amount of inventory goods directly reflects the use of the company’s current assets. If the inventory is too high, the normal operation of the liquidity will be threatened, and the inventory amount is directly proportional to the inventory and its unit price. Therefore, in order to accurately calculate the actual profit and loss of the enterprise , Must pass the inventory.
- Verify the effectiveness of product management. Through the inventory, you can find the problems in the operation and management, and solve the problems to improve the operation process and operation methods, and improve the quality of personnel and the management level of the enterprise. The system can generate an inventory plan based on the warehouse area.
Specific steps
- Warehouse management personnel use the handheld terminal counting machine to count the goods in the warehouse area: scan the warehouse bar code, the goods bar code, and enter the inventory quantity of the goods.
- After all the goods have been counted, the actual inventory quantity can be obtained. At the same time, a difference report between the system inventory and the actual inventory is generated. If the inventory difference is within the acceptable range and the manager confirms it, the system will update the inventory data according to the inventory result, otherwise it needs to be re-stocked.
- After the inventory is completed, compare the actual inventory and the book materials to form an inventory loss and profit table. According to the inventory surplus and inventory loss table, carry out inventory surplus storage and inventory loss out of storage, so that the book is consistent with the physical object. Advantages when inventorying goods under barcode-Paperless inventory operation-Scan the barcode of the cargo location to quickly check the inventory information of the goods on the shelf-Ensure the consistency between the system inventory and the actual inventory-Accurate inventory data can increase inventory turnover, Reduce operating costs
- Transportation management, the warehouse manages the physical objects according to the location, and the system provides the transfer management function, which can realize the mutual movement between the locations, so as to achieve the accuracy of the goods between the locations, and provide convenience for the custodians to deliver goods. . Enterprises can move the database according to the required requirements. Specific operation steps 1. Before moving the warehouse, the warehouse clerk first determines the goods to be moved, scans the barcode of the corresponding goods, and then enters the new storage location; 2. When moving the warehouse, the staff scans the corresponding goods and clicks them out, and Enter the destination warehouse into the PC system. 3. After the warehouse is moved, the warehouse management personnel determine whether the warehouse is moved correctly. If it is not correct, check the cause of the error and correct it accordingly.
Advantages of using barcode technology for library transfer management:
- Strong data reliability, almost zero error rate, to ensure that the barcode is scanned correctly, and to reduce human error input;
- Cost saving: paperless operation reduces paper expenses;
- Improve employee work efficiency, fast and efficient logistics loop;
- Effective utilization of inventory space reduces operating costs;
- Increase the accuracy rate of inventory;
- Statistical reports of various current and historical affairs provide accurate and useful information for decision-makers.
Three, modern warehouse management system characteristics under bar code technology
Warehouse management under bar code technology can eliminate the inaccurate distinction when a material has several suppliers in the past; it can prevent a one-to-one correspondence when a material has several unit prices. Barcode management is now carried out, and the ins and outs of each material can be clearly understood, thus effectively controlling the chaotic phenomenon of material management.
At the same time, cargo management can be done: fast, convenient, accurate and timely. Now when the materials are put into the warehouse, only the warehouse staff need to scan the barcode and put it into the warehouse according to the contract, and then print the scanned information out of the warehouse and transfer it to the finance. This greatly reduces the work pressure of the staff. When the materials are distributed, it is very convenient and fast. You only need to scan in the bar code of the recipient, the bar code of the material, and fill in the quantity. There is no need to fill in text in the whole process, which consumes little time and greatly improves work efficiency. It can accurately and timely reflect the dynamic situation of inventory materials, and the changes of materials in and out of the warehouse can be reflected anytime and anywhere, so that the accounts and materials are consistent, which provides a reliable basis for the reasonable preparation of materials procurement plans. Effectively control the shortage of inventory or repeated purchases due to inaccurate information.
- The application of bar code technology in warehouse management realizes the automatic collection of data, and eliminates the steps of manually writing receipts and sending them to the computer room for input, which greatly improves work efficiency.
- Solve the shortcomings of outdated and lagging warehouse information.
- Solve the problem of inaccurate manual receipt information (mainly copying errors and typing errors).
- The large amount of paper text information required by the receipt is converted into electronic data, which simplifies the query steps in the future. The cargo coding management system produces barcode labels according to actual needs and barcode coding rules, and pastes them on the cargo packaging boxes as the basis for barcode identification.
Four, the key factors of the storage system
First, the method of data transmission: through the communication interface between the handheld bar code input terminal and the computer, directly call the data transmission function in the corresponding program of the computer management system, instead of starting the data communication program, the transmission content can include : Product barcode, name and quantity. The data transmission function includes data download and upload.
Second, data download: data download is to transfer the product information that needs to be confirmed by the handheld bar code input terminal from the computer to the handheld bar code input terminal. The download of data can easily display the name of the commodity currently read into the barcode and the quantity to be confirmed during data collection.
Third, data upload: data upload is to transfer the collected product data to the computer through the communication interface, and then convert the data to the corresponding database through the processing of the computer system. Fourth, data deletion: After the data in the handheld bar code input terminal is transmitted to the computer system, the data needs to be deleted, otherwise it will cause the data to be read in again and cause data errors. In some cases, the data may be transmitted to the computer multiple times, and the data can be deleted only after the data is confirmed to be invalid. Details to be paid attention to 1. Document number
In the process of goods circulation, the data of different customers and different batches are usually distinguished by the single number. In general, the handheld barcode input terminal may store the product data of several documents at the same time. It is necessary to distinguish by the document number, both inbound and outbound. 2. Avoid repeated reading
In the process of data collection, there may be repeated readings of the same product, which needs to be screened to ensure the correctness of inbound, outbound, and inventory.
V. Economical and easy-to-implement warehouse management plan
This program can make a written report for every kind of goods and every location in the warehouse, and can periodically inventory the warehouse area. This kind of scheme is very practical for the commodity inventory of the retail industry, the medicine inventory of the hospital, etc.
When designing a specific plan, different software and barcode equipment should be selected according to different requirements. For example, you need to know:
- Does the customer require continuous communication between the barcode scanner and the host?
- Should the data be processed in batches?
- How much data is collected in a day?
- Is it continuous scan or timing scan?
- How often should the results of data processing be reported, hourly, daily, or monthly to send inventory data to the database?
- How is the physical location in the warehouse identified?
- When and where the barcode label of the data item is used by whom, whether there are other users to scan after the label leaves the library, etc.
Operation process: The warehouse clerk scans the cargo location with a handheld barcode terminal. After scanning the cargo location number, scan the corresponding item number (such as the part number) of the goods on it and enter the quantity of the item. Then scan the second cargo space and the goods on it, and repeat the above steps until all the goods in the warehouse are counted. Then the data collected in the bar code terminal is transmitted to the PC through the communication interface.
All the software used in the system is divided into two parts: one part resides in the barcode terminal, and the other part resides on the PC (or other minicomputers, host). The software in the bar code terminal only completes the data collection function, which is relatively simple, and most users can program by themselves. The software in the PC should include a database system and warehouse management software.
The requirements for the barcode terminal that completes the data collection function are not high, and complex functions (such as the ZZ9801 machine) are not required. There is a 4-line xl6-character display to display the collected data and program menus; a keyboard to input the number of items; a certain capacity of data storage (256KB~512KB or greater capacity); the barcode scanning part can use pen type (Such as HP305 light pen), CCD type (such as Cipher Lar l021 CCD), laser gun type (usually laser gun should be selected, because light pen and CCD scanner are both contact scanning, not suitable for warehouse operations-editor’s note); one RS -232 serial port is used as a two-way communication interface with PC. The program in the terminal is downloaded by the PC, and the data collected by the terminal is uploaded to the PC.
When warehouse operations increase, the number of barcode terminals can be increased. However, the PC does not have to be increased. Of course, the configuration of the PC must be appropriate, such as a 486 or 586, a hard disk of more than 500 megabytes, and so on.
In addition, the system needs to be equipped with a bar code printer to print various labels: labels for cargo locations and shelves; labels for item identification, and indicate the batch number and quantity. Of course, we must first decide how to label these items, whether to label each item, unit, box… or other solutions. In addition, warehouse staff must be identified to facilitate management. As for how to design the bar code, how to design the label format, etc. are all completed in the planning stage.
The advantages of this system are low cost and flexible system. Users who are not familiar with barcode technology can start with this.
VI. The management plan of the main warehouse
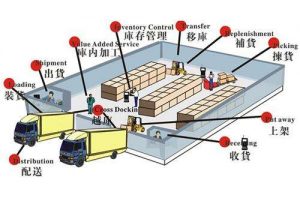
Another example is the management system of a main warehouse. The building area used by the main warehouse is 3,200 square meters and the height is 5.5 meters. There are 5 roadways, including 4 double-extension roadways and one single-extension roadway; the size of the cargo space is about 1.5×1.5×1.1 meters, a total of 3000, and the highest level is 7; the size of the cargo box is 1.2 X0.7×0.7 meters , Gross weight is 215 kg; the size of the pallet is 1.25×1.47×0.08 meters, and each pallet is placed with 2 containers. The throughput capacity of the warehouse is 120 cargo spaces per hour; 80 cargo spaces per hour for inbound and 40 cargo spaces per hour for outbound.
Warehousing operation: After the cargo box is unloaded from the container by the trailer, the trailer is used to place 2 boxes on the empty pallet of the warehousing platform in the designated direction at a time. The pallet number of the goods is identified by the barcode recognition system, and the computer system controls the conveying system to send the pallets to the storage compartment of the designated lane, and then the roadway truck sends the boxes on the pallets to the designated cargo space.
Outbound operations: input data into the warehouse management system according to the outbound operation sheet, issue outbound operations instructions according to the outbound principle (such as first-in, first-out, etc.), and the roadway trucks will follow the instructions to the goods on the designated cargo space Send it to the outbound cargo compartment, and then send it to the designated outbound station by the conveyor system.
The system uses a fixed bar code reader (such as TLMS-3500 RV) to automatically identify the pallet numbers passed on the inbound/outbound conveyor system, and upload the signal to the computer system in real time. After confirmation, the system will command the conveyor line Send the boxes on the pallets into/out of the corresponding lanes and storage locations.
The system is centered on a computer monitoring machine, and is directly connected to the conveying line control system through the RS-232 port. Connect the outbound barcode reader through an 8-port communication manager, and directly connect with the serial port module of the programmable controller; connect the inbound and laneway barcode reader through a 16-port communication manager, and directly communicate with it through the RS-232 port The monitoring machine is connected.
Using this system can improve the accuracy of goods out/in, ensure the high quality of products, and can also change the labor intensity of manual handling in the original system. Low work efficiency.
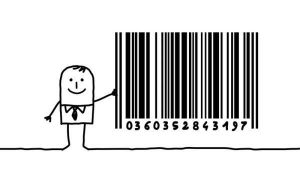
Barcode technology is like a link that connects the information that occurs at all stages of the product life cycle, and can track the entire process of the product from production to sales, so that the company can It is in a favorable position in the fierce market competition. And bar code can ensure the accuracy of the data, the use of bar code equipment is convenient and fast, and the efficiency of automatic identification technology is incomparable with the keyboard.
Sharp Electronics Co., Ltd. of Japan has adopted a barcode-based warehouse management system for four years. The number of warehouse operations has increased by two digits, but the number of personnel has not increased, and the inventory accuracy has reached 100%; the difference between delivery and purchase operations has dropped to zero. Moreover, some labor-intensive jobs have also been compressed. In the past paper-based operations, about 200 errors occurred every month in terms of delivery and storage. After an error occurred, it would often take months to track these differences to avoid expanding their impact. Now when each item of goods enters and exits the warehouse, the operator immediately uses a handheld CCD laser gun to read the barcode on the goods, and sends the data to the computer through the data collector in time; while some barcode readers are directly installed in the On the elevator, errors are avoided.
In modern society, the market economy determines whether the warehouse status is not indispensable or not, but the important transfer of commodity circulation between the market and modern enterprises in the market economy and the necessary infrastructure for warehousing. Warehouse management realizes modern management methods. Barcode technology is a priority method to ensure the optimization of warehouse operations, make full use of warehouse space, provide customers with high-quality services quickly and conveniently, and earn value-added foreign exchange.
Example: Mitsubishi Heavy Industries’ products are sold all over the country. There are many varieties and large quantities of goods shipped every day, and the workload of the finished product warehouse is very large. In order to ensure the accuracy of the goods out of the warehouse and improve the quality of management, Mitsubishi Heavy Industries has adopted a barcode warehouse management system.
This system uses a handheld laser scanner and barcode technology to collect a large amount of goods information in an instant; and with the help of special computer software, it can quickly check the shipment number, customer name, invoice number and Model, time, sales area and other information to ensure the accuracy of the goods out of the warehouse. It greatly simplifies the working procedures of warehouse clerk, reduces shipping time and error rate, and improves efficiency.
Applicable scope of warehouse management
The warehouses of factories, shopping malls and other units and enterprises are very suitable for units with frequent purchases and shipments, large quantities and many varieties.
Main advantages
- Precise management, practical functions; meet the requirements of most modern warehouse management;
- Convenient operation and simple maintenance; warehouse keeper can be on duty after simple training;
- Adopt advanced barcode recognition technology to reduce human errors, and simplify the tedious work of counting, checking, and entering accounts into a single sweep;
- Convenient inquiries, no need to turn over thick shipping orders, just click on the computer monitor, use the mouse to click the product model, the dealer is clear at a glance, daily, weekly, monthly, annual, any time of delivery Data can be displayed and printed after counting;
- All data can be backed up, so you don’t have to worry about viruses or broken machines;
- Simplify work procedures, reduce work intensity, and improve work efficiency;
- The whole system, well-equipped and affordable, is suitable for warehouse goods management of various enterprises.
Conclusion: The use of barcode technology in warehouse management has strong practicability and applicability. Integrating barcode technology into warehouse management can effectively improve warehouse management efficiency, reduce management risks and pressures, and reduce enterprise warehouse management. Costs and increase corporate profits. Compared with traditional warehouse management methods, modern warehouse management under bar codes has incomparable advantages.
References:
- [1]. Jiang Changbing, Bai Lijun, Wu Chengjian “Warehouse Management Strategic Planning and Operation”
- [2]. Zhu Rongtao, Wang Lizhong “Research and Application of Barcode Technology in Modern Warehouse Management”
- [3]. Lin Zhihua “New Requirements for Modern Enterprise Warehouse Management”
- [4]. Gao Xueping “Analysis of the Upgrade from Traditional Warehousing Industry to Modern Logistics Industry”