Automated production has become one of the current development trends due to the advent of the Industry 4.0 era, and traditional manual packaging and manufacturing methods can no longer meet the ever-changing needs of the current market. Under this circumstance, the application of automation and intelligence is gradually moving towards enterprises. With the evolution of the market environment, the future market trend will no longer be a large number of single products, but will focus on small, fast, and customized products. Therefore, the demand for product production is changeable. By realizing the concept of “intelligent manufacturing”, costs can be reduced and product value can be improved. For example: the introduction of automated equipment in the production line or the logistics packaging section can not only reduce the errors that may occur in manual operations, but also increase the flexibility of production. At the same time, it will also increase production yield and profit, and increase the added value of the enterprise.
At present, the intelligent automation transformation has gradually stepped onto the track, stepping into the layout of automated production as soon as possible, so that enterprises and the market can keep pace with the times and maintain market competitiveness.
Successful case of TSC automatic packaging and labeling:
Background:
Meukow is a well-known French Cognac winery located in the Martha Distillery near French Cognac, which can produce nearly 6,000 bottles of wine per hour. The production site includes six bottling lines with a total capacity of 15 million bottles and nearly 18,000 hectolitres of cognac, brandy and other spirits. After the bottles are packaged and labeled, the products will be shipped to retail stores and mass merchandisers in France and around the world.
Improve performance:
In order to achieve high productivity, Meukow is looking for a high-performance solution that can be integrated into the bottling line and has a complete automated labeling process.
Solution:
Developed by LRI and executed by ARCOCEAN, which has been cooperating with TSC and Meukow for more than 15 years, this solution allows Meukow to integrate the labeling process into the bottling line in a fully automated manner.
This solution integrates a new TSC PEX-1000 print engine installed at the end of the bottling and packaging line. This excellent performance printing engine can quickly print roll labels, greatly reducing the time to complete the packaging and sticking target operation. With a complete and compatible structural design and industry-wide GPIO interface, it can be easily integrated into any printing and labeling system.
After the PEX-1000 prints the label, the automatic arm will stick the label on the box, and then deliver it to Meukow’s retail stores in France and around the world. This system has been partially improved, including an extended labeling arm that has been adjusted to perfectly match various box sizes, and a buffer that can adjust the label output time to make it consistent with the speed of the conveyor belt.
Under the successful installation of a brand-new printing and labeling system, Meukow has greatly increased its production capacity by fully automating the labeling process.
Now, in the new fully automated packaging production line, the preparation and labeling of 2,000 packaging boxes per hour can be completed. Compared with the original semi-automatic production line, which is limited to 150 packaging boxes per hour, the production efficiency can be described as Significantly improved.
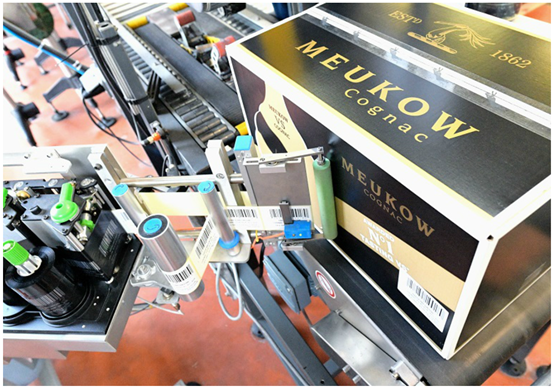
Benefits:
- High-performance printing and labeling solutions
- Easily integrate PEX-1000 print engine
- High-speed automated labeling system
- The production capacity of the bottling and packaging line has been increased by 13 times
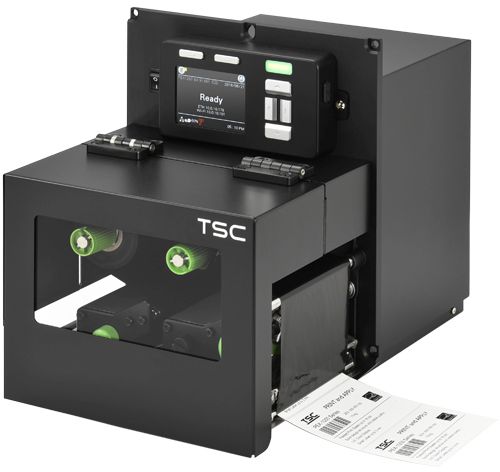
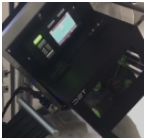
- 600 DPI high resolution is suitable for high-precision content
- Complete GPIO (DB15F) application interface, which can be easily connected to existing printing and labeling equipment
- Excellent efficiency: up to 18 IPS per second, the printing speed is the highest among similar products
- Precise label positioning can support labels as small as 5 mm high
- Back-end pull-out and modular design, convenient and easy maintenance
- Aluminum alloy casting mechanism structure, lightweight and stable
- Large capacity: 512 MB Flash and 512 MB SDRAM memory
- Support optional wireless connection mode: optional Bluetooth and wifi connection to support various projects or various changing needs
- Support various labeling applications: